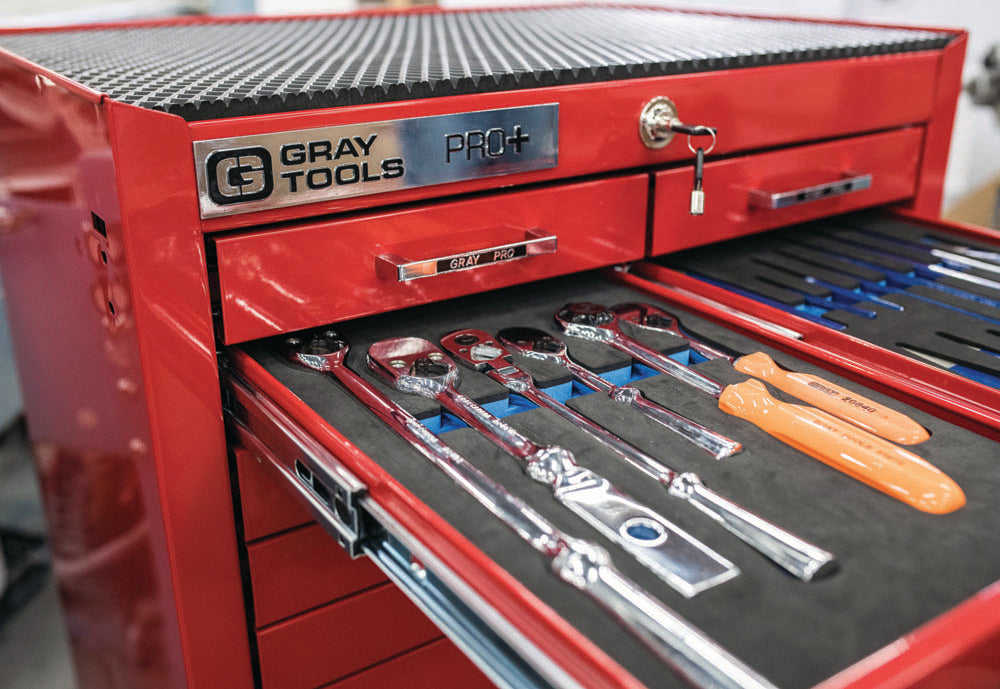
How to Organize Your Tools inside Your Toolbox
- Gray Tools Official Blog
- 05 Mar, 2020
Are you constantly digging through your toolbox drawers looking for the right tool for the job? Do you feel you spend more time looking for tools than performing the actual job?
Most of us understand the benefits of having tools that are organized and easy to find. Taking the time to actually organize your tools is more difficult. After a hard day at work, it is much more convenient to just throw the tools back in the box, go home and relax.
Convenient, but not very productive.
A cluttered toolbox leads to wasted time and frustration. Here are some of the negative consequences:
Decreased productivity - for professionals who use tools to make a living time is money. Having a cluttered toolbox means you spend unnecessary time looking for the tool or size you need, thus delaying project completion.
Redundant tools - if you do not see the tool, you forget you have it and tend to improvise with the wrong tool or buy a new one. As a result, you might end up with many duplicate and triplicate tools and sizes. Backup tools can be convenient and useful, in case the original breaks or doesn’t perform properly; however spare tools should be kept in a separate toolbox (also organized) and only be used to replace the original.
Lost tools - lack of organization makes it difficult to keep track of your tools, which can be easily lost or even stolen. Quality tools are not cheap, so every lost tool is another dent in your budget. Moreover, in many workplaces tool control and inventory is critical, which leaves no room for lost or misplaced tools.
Five Rules for Organizing Your Tools
Tool organization starts with the type of storage you use. If you are just starting out and do not have any storage for your tools, the first step is to decide on the type of tool storage best suits your needs.
Top chests and roller cabinets are very common tool storage options for workshops, garages and industrial settings, where the need to move tools offsite is minimal. With this setup, you will have many drawers to accommodate your entire tool collection. This is beneficial, however it comes with a great need for organization.
Stackable cases, canvas totes, rolling cases, and portable boxes are mainly used by professionals who need to carry their tools around and work remotely on location. These are also great options for those who lack space to accommodate a rolling cabinet, or simply do not own enough tools to justify one.
Before we explore the various options to unclutter your toolbox, make sure you follow some basic organization principles:
Separate tools by type and/or function, and group them together for easy access. Usually roller cabinets and top chests come with narrow drawers that can be used to group tools from the same family together, such as ratchets, files, and pliers.
Label everything. Many tool storage options have dedicated label holders. Labeling provides a quick visual guide of where the tool you need is located before you have to open any drawer or lid.
Get rid of any tool that is no longer safe to use. Tool reorganization is the perfect time to inventory your tool collection, and remove any worn out tools, tools with missing parts, or one that can simply no longer perform the job it was designed to.
Plan your storage according to the size and shape of your tools, as well as frequency of use. Heavier and bulkier tools should be placed in the bottom drawer of the roller cabinet, which is usually deeper. Moreover, having the tools you use frequently grouped together and easily accessible saves you a lot of time when working.
Keep spare tools in separate boxes. Almost any professional will end up with duplicate tools. These extra tools should be kept in a separate location and used only when the original is lost or no longer functioning.
Tool Organization Solutions
Drawer liners are suitable for roller cabinets and top chests and prevent the tools from rolling inside the toolbox. They also limit the amount of grease and grime reaching the bottom of the drawer, and prevent the tools from scratching or damaging the drawer.
These are especially suitable for long tools such as speeders and extensions that are otherwise difficult or place in organizers and racks. That being said, other tools such as wrenches, screwdrivers, and pliers can be securely held in place, by a good drawer liner that has just the right amount of tackiness.
A good drawer liner is thick enough to act as a cushion for your tools, easy to clean, with some offering enhanced protection against corrosion.
Small parts organizers are suitable for all tool storage options and as stand-alone units. They are used to hold and organize small parts, components and tools, such as nuts and bolts, washers, crowfoot wrenches, and small sockets. These organizers come in a variety of shapes and sizes, usually adjustable to accommodate a variety of tool shapes and sizes. They are usually made of plastic, which makes them light and easy to move around, and provide an area for labeling. Some organizers feature an interlocking mechanism to secure them in place.
Individual tool organizers are suitable for all types of tool storage and come in handy when having to organize tools that come in many sizes and styles such as sockets, wrenches, and pliers.
Most popular organizers include rails (used mostly for sockets), trays, racks and holders. Each system has its advantages and disadvantages; the perfect one is the one that best suits the tools you own.
When choosing a tool organizer, make sure the model you plan to buy can actually accommodate the tools you have. For example, some socket organizers cannot accommodate all sockets, and you will be left with a few that need to be placed somewhere else, which defeats the purpose of organization.
Product packaging: when deciding for your next tool set, pay particular attention at how it comes packaged. In some cases, product packaging is designed to offer a viable storage and organization option.
Many socket sets come in blow mold cases with removable lids, designed to fit nicely in the toolbox without the need for extra organizers. Other manufacturers include socket rails (metal or plastic) with every socket set.
Many wrench sets come with rails or plastic holders included, while pliers and screwdrivers sets may also include storage racks to keep the products neat and organized.
Premium sets offer another convenient solution to store tools in foam cut-outs, ready to be placed directly inside the toolbox.
While tool organizers are great bonuses, they are specifically designed to hold only the sizes and shapes included in that set. If you are looking for organizers that are universal and can accommodate many sizes and shapes, product packaging is not a good option.
Custom foam organizers are the latest trend in tool organization, embraced by many professionals and corporations for good reasons.
First, foam cut-outs can accommodate many different types of tools, which come in handy when you have tools that are used more frequently, or a group of tools used for a particular jobs. Instead of opening many drawers to gather tools, the foam organizers can hold all the tools in one drawer.
Second, foam organizers are made using 3D design and multiple layers of high-density foam in contrasting colours (the bottom layer being a bright color such as light blue, red or orange), making it easy to identify missing tools. The light colour acts as a visual indicator so you can spot missing tools quickly. This is particularly important if you are working in a FOD or 5S environment, where keeping track of your tools is mandatory.
Lastly, foam organizers are precisely created using CNC routers to provide a tight fit for each tool, keeping them neatly organized. This allows you to grab the right tool fast, and return it in to the same spot when you finish the job. That way you can work more efficiently, without pulling all drawers to look for the tool you need.
Keeping your tools organized is the first step in a productive career. While the options above are able to solve most professionals’ needs, the best method is that one that works for you and your tools.
I like how you mentioned that the type and kind of storage you’re using is the starting point for tool organization. My father is thinking of getting foam inserts for his toolbox at work because he noticed the other day that his expensive drills were getting damaged from other equipment rubbing against them. It seems like a good idea for my father to think about hiring a reputable professional to help customize the foam he needs to place his tools in so they’ll be protected as best as possible. https://www.aerpak.com/foam-inserts.html
Great advice on tool organizing. The great thing about doing this, and yes it takes some work, is that at the end of the day it is so easy to scan to make sure every thing has came home. I learned this many years ago after buying a set of punches and chisels in a roll up pouch and made a point of replacing them after use. I have used them a lot and 45 years later I still have them all!